Member? Please login
The Minami Soma Robotics Hub
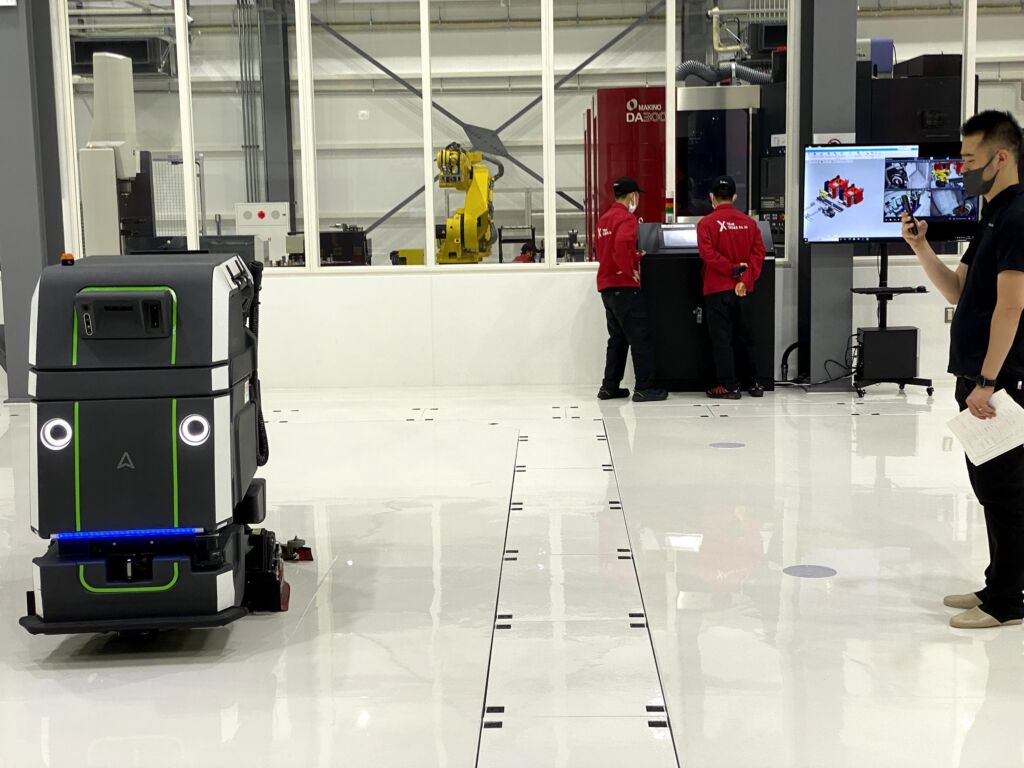
Written by BCCJ
October 7, 2022
Member News
By Simon Yates, Avidbots
It has now been 11 years since the Tohoku earthquake. While recovery has been a challenge, Minami Soma, a city close to the Daiichi Power plant, has used that time to reinvent itself as a robotics technology hub.
Experience gained using robots in the initial relief effort proved helpful to developers trying to commercialise robotics technology. Today factories and warehouses are beginning to use robots to address labour shortages, with mobile robotic buggies called autonomous mobile robots (AMR) that are used for a variety of tasks including transporting materials around a facility.
Automation experts Robotcom&FAcom (RFA) opened their Smart Factory in Minami Soma in spring 2021. Aside from managing their own production lines, they help other companies to modernise their factories. British Chamber of Commerce in Japan (BCCJ) member Avidbots spent this summer operating their Neo 2 fully autonomous floor scrubbing robot at the foundry, integrating Neo into the RFA production process.
With any new piece of technology, integrating a robot into an existing facility and operation can pose a variety of challenges. With that in mind, safe cohabitation and collaboration between the robot and facility operators is paramount.
Since 2011 Japanese and British firms have helped develop vision systems and artificial intelligence (AI) to carefully guide AMRs around facilities and unlock their true potential.
While there are barriers for users to overcome, for many it’s the initial cost of investment. Few companies are rich enough to build a new factory simply to accommodate robots. The fear then is that small and medium-sized businesses (SME) in Britain and Japan could increasingly fall behind their more modern and cash rich competitors.
RFA’s production manager Keiichi Yoshida comments that:
“Building a Smart Factory from scratch is effective and relatively simple to do, but it is also very costly. However, there are ways and means to make existing factories smarter and more productive.”
The trick is to gradually integrate robots into operating factories that may never have been built to accommodate them. Encouraging a slower, steadier robotics evolution is easier said than done, but it is partially responsible for Minami Soma’s success in robotics development.
Canadian AMR manufacturer Avidbots understands this very well, having deployed over 1,000 Neo robots in “real world” environments like the RFA factory. Operating outside of a demo lab means coping with harsh operating conditions and unpredictable — and potentially mobile — obstacles. In fact, Neo facilitates the evolution by cleaning factory floors of grease and swarf so that other AMRs can be used in greater safety.
To learn more about the Minami Soma tech hub and Avidbots Neo, visit one of the following events occurring throughout October:
- International Robot Development conferences ROSCON2022 and iROS2022
(Kyoto International Conference Center, 19-27 October) - Japan Robot Week 2022
(Tokyo BigSite, 19-21 October) - Building Maintenance and Clean Expo 2022
(Tokyo BigSite, 26-28 October)
Additionally, visit www.avidbots.jp for more to see Neo in action, learn more or to schedule a demo.
=====